Paper No. 13 MANAGING CORROSION WITH PLASTICS VOLUME VIII THERMOPLASTIC LINED PIPE FOR CORROSIVE CHEMICAL APPLICATIONS
ABSTRACT
Pipe lined with thermoplastic resins have been successful in overcoming the corrosion problems of a wide range of applications encountered in the chemical, petrochemical. and semiconductor industries. This paper discusses the use of PP, PVDF, ECTFE, and PTFE lined pipe in these industries. Applications for these materials and their limitations are discussed.
INTRODUCTION
The first lined pipe appeared in the U.S. in the late 1940's. The first material used was Saran (PVDC). As more demanding applications developed with higher temperatures and more corrosive chemicals other materials such as chlorinated-polyether, polypropylene (PP), polyvinylidene fluoride (PVDF), ethylene-chlorotrifluoroethylene (ECTFE) and perfluoro alkoxy (PFA) appeared and found their area of application.
Advantages of Lined Pipe Lined pipe has the following advantages:
Lined pipe represents one of the most widely used forms of a composite structure. The mechanical properties and low cost of carbon steel are combined with the chemical resistance of the plastic lining material. The properties of the liner material such as chemical resistance and continuous service temperature can be readily tailored to the specific conditions of the application while still maintaining the use of low cost steel for the mechanical and impact properties. The excellent release properties and non-fouling properties of some plastic materials reduce fouling, the resulting pumping energy losses, and required downtime for clean out. Lined pipe is safer from a mechanical abuse standpoint than self-supported plastic pipe. Self-supported plastic is not permitted in critical applications by some chemical companies for safety reasons. Plastic pipe, either lined or self supported, results in improved product purity due to the lack of metallic contamination. This is of particular importance for the semiconductor, pharmaceutical, and fine chemical industries. Plastic pipe is not sensitive to changes in chemical resistance due to process changes from oxidizing to reducing atmosphere as some of the metals are. Plastic pipe, lined or self supported, is not subject to crevice corrosion or chloride pitting as some of the metals are. Significant cost/performance benefits exist for lined pipe compared to corrosion resistant metal pipe, especially considering fully installed cost. Most plastic lined pipe has a built-in gasket eliminating the need for a separate gasket to prevent leaks, simplifying installation and maintenance. The gasketed surface has the same chemical resistance as the liner. Lined plastic pipe can be field installed faster than metal pipe with crews that are properly trained.
DISADVANTAGES The disadvantages of plastic lined pipe are as follows:
The current maximum continuous use temperature of plastic lined pipe is <500°F. The maximum chemical resistance for plastic lined pipe is on the protected inner surface. External corrosion can occur in poorly maintained plants due to poor housekeeping. Creep and permeation are factors for consideration in the selection of a plastic liner material. These two factors are not normally encountered with metal piping. Abrasion resistance of some plastic materials are inferior to metals. Temperature and solids content of the process fluid can significantly affect performance. Plastic lined pipe is more sensitive to non-uniform heat tracing (hot spots) than is metal pipe. Maintenance personnel need to be properly trained as to the proper techniques for field fabrication of non-standard lengths of plastic lined pipe. The performance advantages of plastic lined pipe far outweigh the disadvantages.
DESIRED PROPERTIES OF A LINER MATERIAL
Easily processed into lined pipes, valves, and fittings to permit the supplying of a complete corrosion resistant system. Broad use temperature range. Excellent permeation resistance. Low coefficient of expansion. Low creep characteristics. Good abrasion resistance. Excellent chemical and solvent resistance. Excellent stress crack resistance. Low cost per cubic inch.
- ENGINEERING CONSIDERATIONS
- Lined pipe is made in the U S to meet ASTM F423 F546 F491, F492, F781, or F599 specifications. These industry specifications currently cover pipe and fittings lined with PTFE, FEP, PVDF, PP, PFA and PVDC. These specifications cover:
- Material properties.
- Pipe and fittings characteristics including welds, finish and gasket requirements.
- Dimensions and tolerances.
- Testing and inspection.
- Venting requirements.
- Workmanship.
- The U.S. lined pipe industry, through these specifications and the committees working on their revision and updating, is attempting to furnish you, the end user, with a reliable, cost effective product.
- Lined pipe can be fabricated with either a loose or locked in liner. A locked in liner reduces the effect of the difference in expansion coefficient between the metal and the liner. A loose liner, when extensively thermal cycled, can result in cracking at the flange surface since that is the only place where the liner is restrained. Loose liners tend to roll back and forth at the flanges when heated to an elevated temperature due to the differences in expansion between the metal and liner. Loose liners tend to collapse when operated under high vacuum at elevated temperatures. In addition, loose liners provide a space for gas build-up between the liner and the pipe and resulting corrosion and liner collapse. Weep holes which can be used to initially prevent this problem are readily blocked by paint, rust, and insulating materials. Weep holes can also create problems of structural corrosion of the metal pipe. Weep holes are commonly used with PTFE, FEP, and PFA due to their poor permeation characteristics.
LINER THICKNESS
- Liner thicknesses are typically in the range of .1-.3 inch. The liner thickness represents a compromise between cost, permeation, cold flow, service life, and vacuum performance. A thicker liner will result in lower permeation, longer service life, and improved vacuum performance. Cold flow increases with thickness and so, obviously, does cost.
LENGTH AND DIAMETER
- Standard lined pipe is available in the U.S. in diameters up to 24 inches and lengths of 10 and 20 feet. Lengths longer than 20 feet are not available due to fabrication and thermal expansion problems.
JACKETING MATERIAL
- Lined pipe is commonly sold with carbon steel as the jacketing material. However, ductile iron 304, and 316SS are available as a means of controlling external corrosion. The use of carbon steel is the reason for the -20°F lower limit for the use of lined pipe. As you may be aware, carbon steel pipe becomes embrittled at temperatures below -20°F. The use of stainless steel pipe jackets or other non-ferrous metals permits lined pipe to be used to lower temperatures.
FITTINGS
- For lined pipe to be attractive and viable, a total system is required including tees, elbows, crosses, standard reducing and special configurations. The method of fabrication of the fittings is key to the total system reliability. The ASTM specifies that no welding is permitted on the fitting after the liner is molded into place. Some of the lined fittings on the market do not comply with this part of the ASTM with a resulting loss in reliability.
PRESSURE AND VACUUM LIMITATIONS
- Lined pipe is available in 150 and 300 pound pressure rated pipe. Higher pressure pipe is available on special order. Bonded lined pipe can operate at full vacuum. Vacuum collapse capability of loose lined pipe is dependent on liner thickness.
CUTTING AND FABRICATING
- Each of the suppliers of lined pipe have their own developed techniques for cutting and flaring of their pipe. The technique used with the Fusibond lined pipe is as follows:
- Determine the finished length of the pipe and add to it the additional length required for either a single or double flare. Cut the pipe to the total determined length.
- Be certain that a sharp cutting tool is used. A wheel type cutter is never acceptable as they pinch the steel into the plastic.
- Cut a groove through the metal pipe only, do not cut into the plastic lining, to the required length allowing for the flare.
- Remove the metal sleeve from the liner using a tool such as a pipe wrench being careful not to mar the plastic.
- Thread pipe and attach a socket or threaded flange. The flange must have a chamfer or rounded edge where the plastic makes contact with the inside edges. A vented flange should be used for PTFE or PVDF lined pipe.
- Heat the exposed plastic sleeve using a hot air gun. Heat the flaring die on a hot plate as follows:
- Polypropylene - 250 to 260°F
- PVDF or ECTFE - 275 to 300°F
- PTFE - 525 to 550°F
- When the heated liner is soft and pliable to the touch it is ready to flare. The heated flaring die is then positioned onto the heated liner and hydraulic force applied to flare the liner.
- After flaring a blind flange or plywood face protector should be bolted in place to protect the flared surface from damage.
- For obvious reasons, welding of lined pipe is not feasible since the plastic liner would be destroyed by the high temperatures developed. Flanged connections are the only reliable means of connecting lined pipe. Threaded connections are similarly not possible or recommended.
- INSTALLATION
- The same installation procedures for conventional flanged steel pipe and fittings can be used to install any of Fusibond's piping systems. Pipe hangers, supports, anchors, guides and expansion joints or loops should be in compliance with accepted piping practices.
- End covers should not be removed until pipe is ready to be bolted into position or sealing faces may become damaged or distorted. If covers are removed for inspection, they should be replaced as soon thereafter as possible. Never use heat or a chisel to remove bolts as the plastic face may be damaged. Gaskets are not required with Fusibond piping except when connected to a flange face of another material. Gaskets of the elastomeric type are usually most suitable and should always be approximately the same ID as the pipe. Bolts should be tightened using specified torques as a guide. Use the criss-cross method shown; never clock or counter clockwise. Installation in cold weather may require higher bolt torques.
- When assembling piping, always use new nuts and bolts. Threads must be cleaned and lubricated and washers are suggested under the turned element (head or nut). Bolts should be cross torqued evenly.
- NO WELDING OR FLAME CUTTING should be done close to the metal pipe or fittings unless adequate precautions are taken to prevent their being exposed to excessive heat.
- Vent holes should not be plugged with paint, cement, etc. The vent holes are necessary only with PTFE/PFA to release gases which may be generated at elevated temperatures and become trapped between the liner and housing. If not vented, these gases may collapse the liner. Vent holes are placed under the flanges for safety. This is essential when flange covers are used with hazardous materials.
- To preserve the sealing faces and protect them from damage while not in use, end covers or blind flanges should always be installed immediately on all piping items which are removed from service.
DESIGN AND FABRICATION DEFECTS
- As the old saying goes, "a chain is only as strong as its weakest link". The performance and longevity of a lined pipe system is only as good as the design and fabrication details that went into its construction. Common flaws encountered in commercially available lined pipe and fittings are as follows with the indicated effects:
- Sharp edges, non-radius surfaces -- points of stress concentration with a resulting tendency to stress crack on thermal cycling. See Fig. 1.
- Welding after liner insertion - severe thermal damage to the plastic liner. See Fig. 2.
- Poor weld penetration, usually 50% or less - resulting in poor mechanical reliability of the fitting or pipe coupled with thermal damage to the liner. See Fig. 2.
- Thin or non-uniform lining - permeation occurs at the thinnest spot in the lining. See Fig. 1.
- Highly stressed lining -- tends to either cold flow or stress crack. See Fig. 1.
- Foreign particles in plastic liner -- need for ongoing QC. See Fig. 3.
- Non-bonded liner -- tends to cold flow and collapse under high vacuum or as "bulge" due to permeation.
- Non-tested liner -- supplier should perform final QC on all lined components and not rely on statistical acceptability.
- "Mechanical" picked lining -- reduces the effective liner thickness due to the metal projections embedded into the liner.
- Sharp projections, blow holes in pipe or fitting --quality of the lined pipe or fitting is only as good as the metal part that it is being inserted into.
- In the event of repeated field failures an end user should consider sectioning of the failed fitting to determine the cause of failure. Continued replacement is not always the answer.
TESTING AND QC PROCEDURES
- The procedures used to furnish quality assurance by this company are as follows:
- All pipe and fittings are visually inspected for any imperfections prior to lining.
- Interior of pipe and fittings are smooth, clean and free of burrs or other imperfections. All corners in contact with the lining are radiused and the welds ground smooth.
- All welding operations are performed prior to lining.
- After lining, all pipe and fittings must individually pass a minimum of 10,000 volt non-destructive electrostatic spark test.
- That portion of the lining forming the flange gasket sealing surface must be free of scratches, dents or any defect measuring greater than 10% of the lining thickness.
- After thorough inspection, all fittings and pipe spools must have the plastic raised face protected with minimum 1/2" thick plywood end covers bolted in place. The covers should not be removed until the pipe or fitting is ready for installation. If protective covers are removed for inspection, they should be replaced as soon thereafter as possible.
- APPLICATIONS FOR LINED PIPE
- PVDC (Saran) was the first plastic lined piping material introduced to the marketplace. It found a niche in the steel industry in acid pickling handling hydrochloric and sulfuric acids. Deionized water service for the food, pharmaceutical, and semiconductor industries were also areas of application. As temperatures and performance requirements increased, some of these applications declined.
- PP was the next plastic lined piping material introduced. It has taken some of the applications for PVDC. It is now used in the steel industry for acid pickling at temperatures too high for PVDC. Food processing, handling. materials such as fructose and other syrups, is an area of application for PP. Water and waste water treatment is a large area of application for PP.
PVDF is much more chemically resistant than the two preceding materials. PVDF is widely used to handle aggressive chemicals such as strong acids, chlorine, and bromine. It is widely used at this time in the semiconductor industry to handle high purity water and process chemicals where both chemical resistance and non contaminating characteristics are important. PVDF is also widely used in the pulp and paper industries. ECTFE is being used in applications similar to those with PVDF where higher temperatures or concentrations make PVDF marginal. ECTFE is used to handle chlorine, caustic, hypochlorite, and sulfuric acid. It is being used for these applications in the chlorine, pulp and paper, and chemical industries. PTFE and PFA are being used to handle a wide range of chemicals generally above 300°F. Industries using these materials include chemical, petrochemical, food, pulp, chlorine, and semiconductor. SUMMARY AND CONCLUSIONS
Commercial lined pipe has been available in the U.S. since 1940. A range of materials are now available to cover temperatures up to 500°F handling a wide range of chemicals. Lined pipe is cost and performance competitive with stainless steels and high nickel alloys. Additional advantages for lined pipe include improved product purity due to the lack of metallic contamination which is of particular importance in the semiconductor, pharmaceutical, and fine chemical industries.

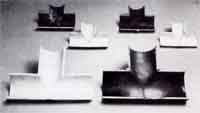
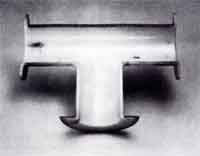
Symposium Sponsoring Societies American Institute of Chemical Engineers American Society of Civil Engineers National Asssociation of Corrosion Engineers Society of the Plastics Industry Society of Plastics Engineers Society of the Plastics Industry-Canada Technical Association of the Pulp and Paper Industry
|